Printing plates
To whom the printing plate production service is addressed
Our printing plates are created to meet the needs of companies in various sectors. During production, we subject the plate to various checks: the primary objective is to guarantee the customer the maximum consistency and quality of the final print result on the chosen support, with respect to the creative packaging idea agreed with the customer.
Among our main customers we have:
Print Buyers requiring converting services for packaging on different products.
Printers who require the proposed services to meet the needs of the end customer.
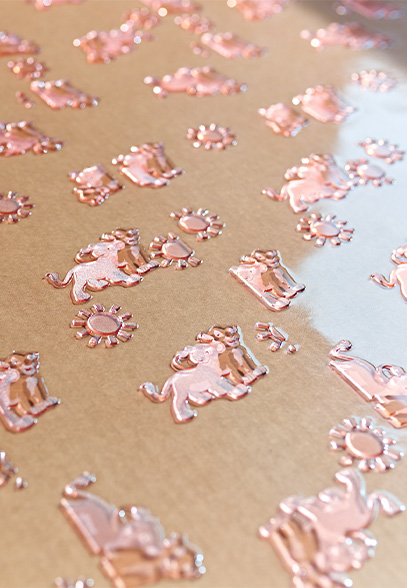
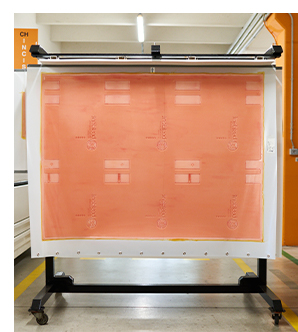
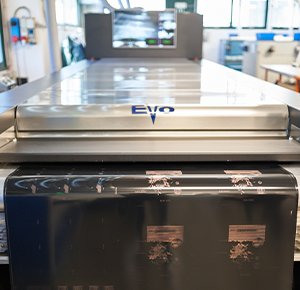
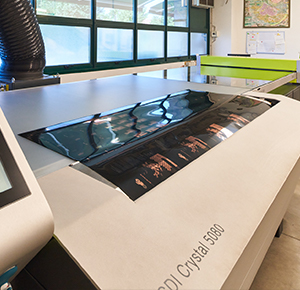
Infinity and Perfect HD Solutions
For big brands, we provide solutions that allow us to offer the most varied types of product: Perfect Print HD Suite and Infinity.
Infinity represents the pinnacle of plate engineering.
Developed by Diaven to ensure maximum image expressiveness for printers and buyers alike, it delivers crisp text, defined images, and vibrant colors for packaging. Infinity is the result of extensive research into printing systems and exemplifies the best synergy between printing plates, substrates, presses, anilox rollers, inks, and adhesives. It combines expertise in plate types, LED exposure performance, screening management, and print performance in conjunction with anilox rollers, inks, and adhesives.
Infinity leverages the innovative XPS Crystal technology, seamlessly integrating primary and UV back exposure.
Unlike traditional UV frames with fluctuating lamp intensity, the XPS Crystal unit uses UV LEDs that require no warm-up time and provide consistent radiation. The simultaneous and optimally controlled primary and UV back exposure produces perfectly uniform digital flexographic plates, regardless of type, production time, or method.
Perfect HD Solutions allows the use of various machines, materials, and plate production methods: Esko’s Crystal LED, Miraclon’s Kodak Flexcel NX, Full HD, and Flat Top in the Plate. This flexibility enables us to:
offer clients a wide range of plate solutions tailored to specific printing needs;
optimize printing results in any scenario through preliminary testing.
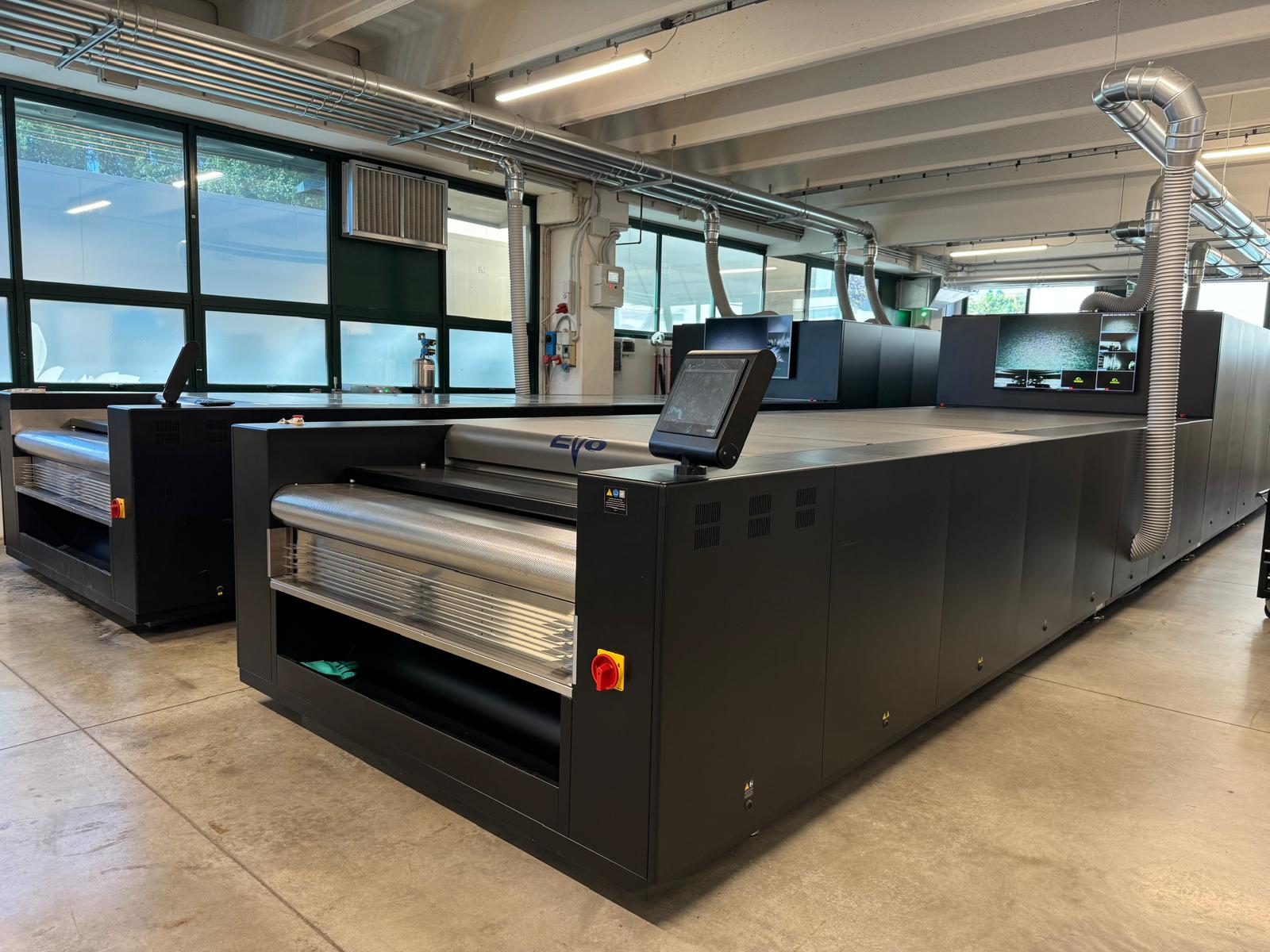
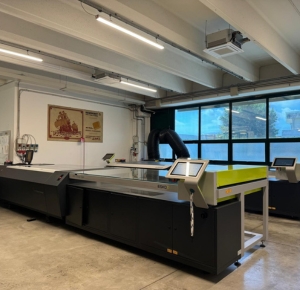
Our Safe Plate Check package
Relying on our professionalism for the production of printing plates means benefiting from a service characterized by efficiency, innovation and an unparalleled customization possibility, declined in our Safe Plate Check package.
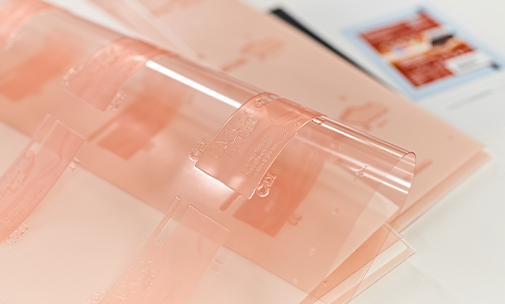
Safe Plate Check includes:

The best technology available, enabling us to produce engravings with a high degree of precision and speed. Thanks to our process automation system, we increase production capacity by 140% on an annual basis, up to 14 hours of continuous operation per day.

Constant monitoring of products, both during parameterization to achieve the set print result, and during the production flow to ensure consistent production at all stages.

Responsiveness and traceability of order status, thanks to a monitoring system accessible at all times: this allows us to guarantee full control of order volume variations and maximum promptness in resolving any urgency.

Data archiving, the information relating to each project is collected on a digital medium and organized to facilitate consultation at all times, simplifying the procedures for checking and modifying parameters.
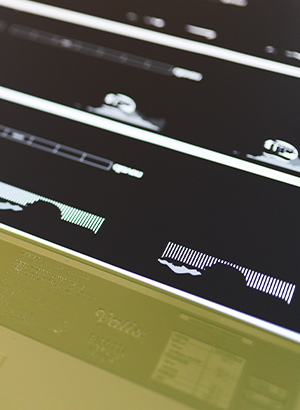
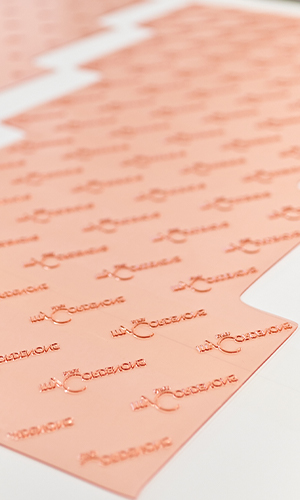
Our printing and letterpress plate technology
For the production of digital photopolymer plates (round top and flat top) in large format (2.03 m x 1.27 m) we use the following technologies:
Crystal LED – Esko XPS
FLEXO HD – Esko HD
We also offer two ESKO CTP (Computer to Plate) systems for digital photopolymer plates up to a maximum size of 127 x 203 cm, both equipped with high-definition optics, along with two ESKO XPS exposure units.
We use two independent plate exposure, developing, drying and fixing lines (127 x 203 cm) and a modular VIANORD EASY TO PLATE™ TWO production line, comprising:
EVO 5 BP PROCESSOR to ensure process monitoring and traceability;
AUTOMATIC DRYER EVO 5 to establish maximum uniformity of plate temperature;
LIGHT FINISHER – STACKER EVO 5 with light integrator for UVA and UVC exposure and 8 drawers to accommodate the finished plates.
The ESKO CDI Crystal 5080 unit enables more efficient production of flexographic plates through remote management of automatic loading. The XPS exposure unit ensures precise and stable dot formation on the plates. Its advanced exposure control allows the creation of next-generation screening patterns, designed to achieve maximum tonal reproduction.
With Diaven’s management system, we can track the status and characteristics of every plate in production. The synergy between the management system and the Device Manager provides the prepress department with all the necessary information to organize production queues efficiently, prioritizing tasks to produce the right plate at the right time. This reduces manual steps by 50% and generates simpler analysis reports. Control systems include ESKO VIEWER, X-Rite eXact, EFI, ENFOCUS, and FLEXO3PRO by PERET.
For the production of letterpress plates we use the Combitype A4 A3 – Cartomac system with water-based development.
Experience before technology
The use of technology for the creation of printing plates is an important part of our work, but even more important is the experience we have accumulated over the years, which allows us to respond to our customers’ requests regardless of the machinery available.